
LORRTEC: crankshaft balancing for V6 V8 V10 V12 engines, and any other type of engine
- Balancing the crankshafts of 4 and 6 cylinder in-line engines
- Balancing the crankshafts of 4 and 6 cylinder flat engines
- Balancing the crankshafts of V6, V8, V10 and V12 engines, with balancing weights on the connecting rod pins.
- Balancing the crankshafts of 1, 2, 3 and 5 cylinder engines in line with balancing weights on the connecting rod pins.
Depending on the case and the needs, we carry out in subcontract the balancing of the crankshaft which is sent to us, even if we do not work on the engine as a whole. We also balance all the crankshafts of the engines that we refurbish or prepare in-house.
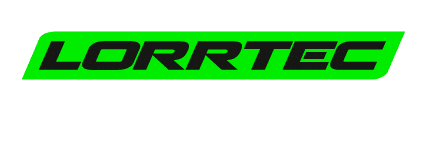
Find our competition and collection engine parts on our online store:
Presentation of the V6, V8, V10, V12, 4-cylinder, 5-cylinder, 6-cylinder in-line or flat engine balancing activity
As an engine manufacturer, LORRTEC must be at the forefront of engine balancing technology, what type of balancing machine do you have?
We have a latest generation SCHENK Pasio balancer. It is a dynamic balancing machine designed for the mechanical industry with software dedicated to balancing combustion engine crankshafts.
What types of crankshafts / engine need to be balanced?
Competition Engine Balancing
It is advisable to balance the crankshafts of the competition engines because they are called to be used at high speeds . For reliability, it is necessary to minimize the loads on the bearings (line bearings) as well as the internal mechanical stresses of the various parts.
Balancing collection engines
The balancing of collector’s engine crankshafts is interesting for limit parasitic vibrations. They are often heavy parts especially on V6 and other V engines (compared to today’s engines) and their finish is not as precise as on modern parts. It is not uncommon to measure significant imbalances before balancing on this type of motor.
Standard engine balancing
The standard motors are factory-balanced by the manufacturers. However , the tolerance (standard) as original equipment is much greater than that which we use (lower balancing class), which makes it possible to further reduce vibrations and engine stresses.
Differences between balancing a 4 cylinder or 6 cylinder in line and balancing a V engine crankshaft:
Balancing V motors:
For V-engines and odd number of cylinders in-line engines (1, 2, 3 5 cylinders) it is mandatory to add balancing weights (“bobweights” in English) to simulate the rotating and alternating masses in level of each connecting rod pin during dynamic balancing on the machine. For this we calculate the masses to be used according to the parts of each engine and we report them on the crank pins of the connecting rods at the time of balancing using machined “bobweights”. The calculation of the masses of the bobweights therefore depends on the reciprocating and rotating masses (connecting rods and pistons) and the balancing factor of the engine.
Balancing of inline (and flat) motors:
The crankshafts with 4 and 6 cylinders in line or 4 and 6 cylinders flat do not require the use of balancing weights at the level of the crankpins of the connecting rods , each crankpin having a crankpin in opposition (symmetrical at 180°).
Balancing is conventionally carried out by removing material.
- Examples of 4-cylinder in-line engines:
- Engines Peugeot 205 to 208 GTi, Renault turbo, Williams, RS, Ford Pinto and Cosworth, BMW M3 E30 etc…
- Examples of 6-cylinder in-line engines: BMW 6-cylinder engines
- Examples of 6-cylinder flat engines: flat6 engines of the Porsche 911
- Examples of flat-6 engines: Subaru GT WRX and STI flat4 engines
Does the angle of the V have an impact?
No , the angle does not affect the balance. This changes the basic crankshaft design but not the dynamic balancing method.
Which V4, V6, V8, V10, V12 engine crankshafts have you ever balanced?
We have tools for most V-engines such as:
- Crankshaft V10 DODGE Viper
- V6 PRV crankshaft with contiguous or staggered crank pin
- Ferrari Dino V6 crankshaft
- Crankshaft V8 FORD Mustang
- Crankshaft V8 FORD GT40
- NISSAN GTR V6 Crankshaft
- Crankshaft V12 JAGUAR XJS
- Crankshaft V10 PEUGEOT F1
- BMW M3 V8 crankshaft
- Crankshaft V8 FORD Cosworth DFV F1
- Crankshaft V8 FORD Cosworth HB F1
Etc..
Whatever the V engine: V6 Peugeot, Renault, Ford, Maserati…, V8 Porsche, Audi, BMW, Mercedes, or American (Mustang, GT40, De Tomaso, Chevrolet Corvette…), we can take care of the balancing and produce the necessary tools when we do not already have them.
QUOTATION
What about very tight V-engines like the 4-cylinder Lancia Fulvia or that of the VW Golf VR6 and other Corrado?
It is advisable to use the same balancing method as for a V6 or V8 engine: it is therefore imperative to mount compensation masses (connecting rods, pistons) during the dynamic balancing of the crankshaft of these engines.
What are the essential parts to balance a crankshaft
For any crankshaft balancing it is necessary to provide us with new screws, the flywheel, the clutch, the pulleys as well as the various sprockets/parts related to the crankshaft.
It is also necessary to make sure to have a perfect centering as well as a setting in unique position between the various parts. We machine centering pins if necessary.
Do you always have to balance a crankshaft with the flywheel and the clutch?
Yes: The crankshaft is balanced on its own first, then we balance the flywheel (and damper it if necessary) independently of the crankshaft in a second step. Finally we control the assembled unit for an optimum result. This method makes it possible to replace a defective flywheel without having to disassemble the crankshaft from the engine in many cases. We also balance the clutch independently for the same reason. However, this is only valid for the steel and heavy clutch mechanisms of older generation engines. Modern competition engines use aluminum clutches (example: Tilton clutches) 140 or 184 mm which are extremely light and already balanced at the factory.
BENEFITS OF LOWER ENGINE BALANCING AND CRANKSHAFT BALANCING
Balancing the mobile coupling (crankshaft, flywheel, damper, clutch, etc.) is essential to reduce engine vibrations, lower the forces on the bearing shells and limit bending and mechanical stresses in the crankshaft itself.
The inertia forces applied to the crankshaft vary according to two parameters:
- the SPEED of rotation: the forces in this case are proportional to the square of the speed. Consequently, competition engines reaching high speeds must undergo particularly careful balancing.
- MASS in motion: the forces are also proportional to the mass in motion. It is therefore important to balance heavy crankshafts such as those of vintage engines from the 70s or earlier. In addition, in the case of competition engines, it is essential to lighten these moving masses as much as possible (connecting rods, pistons, flywheel, etc.) to limit the mechanical stresses during high rotation speeds.
LOW ENGINE LIGHTING: POINTS TO KNOW
Lightening of connecting rods:
Reducing the mass of the connecting rods (within the limits of rigidity and reliability) is always beneficial in order to limit the forces on the bearings and facilitate revving . Connecting rods machined in H (example: Carrillo connecting rods) offer the best stiffness/mass compromise and are therefore to be preferred when fitting a competition engine. Attention: the mass of the connecting rod must be taken into account when balancing a crankshaft in V (or odd number of cylinders). A change in the mass of the connecting rod necessarily requires a rebalancing of the crankshaft in the case of V engines.
Piston relief:
The pistons must be as light as possible (always within the limits of reliability) in order to reduce the forces on the cylinder walls as well as on the connecting rod and its bearing. The use of forged pistons (example: CP Carrillo pistons, Mahle pistons, Wossner pistons, etc.) is recommended when preparing an engine. The forging then machining process guarantees the greatest robustness for a limited mass, with controlled thermal expansion . Attention: the mass of the piston must be taken into account when balancing a crankshaft in V (or odd number of cylinders). A change in the mass of the piston necessarily requires a rebalancing of the crankshaft in the case of V engines .
Lightening of the flywheel:
The lightening of the flywheel is a matter of compromise between engine acyclism and the dynamics of revving . A heavy flywheel will make it possible to filter the torque pulsations due to the combustion of each cylinder (important on a single cylinder for example) but will penalize acceleration at equal engine power. An engine with a high number of cylinders (example V10 or V12) will use a relatively light flywheel, the time between each combustion being shorter and the engine torque more “constant” over a cycle. In the case of multi-cylinder automobile competition engines, the flywheel must be as light as possible. Reducing acylism is then not a priority and it is important to favor the acceleration phases.
IMPORTANT: Contrary to popular belief, a heavy flywheel does not provide torque to the engine . It adds inertia at most and somewhat “linearizes” the return of power during acceleration phases (no influence in steady state), which can provide “traction” in certain cases (off-road or on a motorcycle for example) but in no case of the engine torque…. The torque feel is actually “smooth” rather than snappy on acceleration. The latter being less violent, this reduces slippage, hence the gain in grip or traction in some cases.
To conclude, the lighter the flywheel, the faster the car accelerates at equal power, especially in the first gear ratios (where the acceleration is greatest). The car accelerates faster but will keep the same top speed in all cases (light or heavy flywheel).
Lightening the flywheel is equivalent to lightening the car in terms of acceleration , we gain on the inertia of the car (in rotation), the mass of the vehicle being a translation inertia.
Lightening of the damper pulley:
The damper pulley adds a damped mass (precisely calculated by the manufacturer) in order to minimize the harmful effect of resonance frequencies on the crankshaft and flywheel assembly. Some engines are more sensitive than others to this phenomenon (6 cylinders in line for example) and it is therefore necessary to be extremely vigilant when modifying this part according to each application .
Crankshaft lightening:
The crankshaft is a moving part which must therefore be light, but it must also absorb a large number of mechanical stresses, hence the multiple counterweights which allow (in addition to their role of dynamic balancing) to limit the internal tensions, the bending of the crankshaft and thus the load at the level of the line bearings . A competition crankshaft will have a maximum of counterweights (8 counterweights on a 4-cylinder in-line) while a production crankshaft will be satisfied with fewer counterweights in order to facilitate its production and lower its cost (4 counterweights on a 4-cylinder in-line ). Consequently, the counterweights of a crankshaft depend on the mass of the moving parts attached to it (connecting rod, piston). They are present in order to balance and reduce the dynamic bending of the crankshaft during high revs. (Formula 1 engines use heavy metal inserts to increase crankshaft density in certain areas). It is therefore not necessary to lighten a crankshaft excessively at the risk of reducing its reliability . Ultimately the lightening of the crankshaft is to be considered on a case-by-case basis. It is often wiser to focus on lightening the peripheral parts (flywheel, connecting rods, pistons, etc.) rather than on the crankshaft itself. In the case of V-shaped engines, it is very difficult to lighten a crankshaft without carrying out a thorough dynamic study, otherwise balancing will be impossible afterwards.
The use of steel crankshafts specifically designed for racing (example: Arrow steel crankshafts) is recommended for high-efficiency engines.
Crankshaft lightening:
The crankshaft is a moving part which must therefore be light, but it must also absorb a large number of mechanical stresses, hence the multiple counterweights which allow (in addition to their role of dynamic balancing) to limit the internal tensions, the bending of the crankshaft and thus the load at the level of the line bearings . A competition crankshaft will have a maximum of counterweights (8 counterweights on a 4-cylinder in-line) while a production crankshaft will be satisfied with fewer counterweights in order to facilitate its production and lower its cost (4 counterweights on a 4-cylinder in-line ). Consequently, the counterweights of a crankshaft depend on the mass of the moving parts attached to it (connecting rod, piston). They are present in order to balance and reduce the dynamic bending of the crankshaft during high revs. (Formula 1 engines use heavy metal inserts to increase crankshaft density in certain areas). It is therefore not necessary to lighten a crankshaft excessively at the risk of reducing its reliability . Ultimately the lightening of the crankshaft is to be considered on a case-by-case basis. It is often wiser to focus on lightening the peripheral parts (flywheel, connecting rods, pistons, etc.) rather than on the crankshaft itself. In the case of V-shaped engines, it is very difficult to lighten a crankshaft without carrying out a thorough dynamic study, otherwise balancing will be impossible afterwards.
The use of steel crankshafts specifically designed for racing (example: Arrow steel crankshafts) is recommended for high-efficiency engines.
QUOTATION